OSHA’s Heat Standard Likely to Affect Indoor Manufacturing Facilities | FIRST, VERIFY
This past spring, the Occupational Safety and Health Administration (OSHA) announced its intention to implement a new heat illness standard that will apply to indoor environments. The agency said it has manufacturing facilities in mind, as the rule targets “indoor workers without climate-controlled environments.”
A new heat illness standard is a top priority for OSHA under President Joe Biden, who is seeking to make good on his pledge to be “the most pro-union president you have ever seen.” Public Citizen and Senate Democrats petitioned Biden to encourage the new standard. House Democrats introduced legislation giving the agency two years to promulgate a heat standard. That proposal failed.
Noting that 18 of the last 19 years were the hottest on record and the intensity of recent heat waves have put many employees at an increased risk of heat illness or injury, Acting Assistant Secretary of Labor for Occupational Safety and Health Jim Frederick announced in June that he intends to launch the rulemaking process by publishing a request for information. Frederick remarked that he hopes the agency will have “some very, very good, very thorough stakeholder engagement and involvement” while it develops the rule. “We hope that our request for information is very thoroughly responded to by as many stakeholders as possible.”
The proposed standard is in its preliminary stages and its contents are not yet clear. Requirements in several state standards offer clues. The OSHA standard may mandate break times and require employers to monitor employee acclimatization, as well as temperatures and humidity levels. Such provisions could effectively require costly changes in manufacturing worksites that do not have air conditioning and have a local source of heat, such as a furnace or an oven. Heat levels also can be affected by the presence of many workers at a site, especially if they are engaged in physically exerting tasks.
For example, a factory with employees melting substances like metal or glass would use machinery that can become extremely hot and affect the surrounding environment, regardless of outdoor temperatures. A factory with a furnace operating over 500 degrees causing nearby employees, who may be in heavy personal protective equipment, to perspire heavily, the standard may require cooler temperatures. Minnesota’s indoor heat standard requires employers to measure heat using “wet-bulb globe temperature” (WGBT) index, which is calculated by air temperature, air speed, humidity, and radiation. Permissible heat levels vary by levels of exertion as follows:
“Heavy work” is defined as exerting 350 or more kcal/hr. (kilocalories per hour), which can include heavy lifting and pushing, shovel work. The permissible heat level cannot exceed 77 degrees Fahrenheit.
“Moderate work” is defined as exerting 200 to 350 kcal/hr., which can include moderate lifting and pushing. Its permissible heat level is 80 degrees Fahrenheit.
“Light work” is defined as exerting 200 kcal/hr., which can include sitting or standing performing light hand or arm work. The permissible heat level is 86 degrees Fahrenheit.
In this example, a facility must calculate WGBT and constantly monitor and adjust conditions according to the highest level of exertion by any workers in the working environment. Some manufacturers might find this level of calculation unworkable because of varying or changing production schedules and varying outdoor heat conditions, particularly during heat waves.
There are a few things manufacturing employers can do to help prevent heat-related issues from creeping up, including making sure that employees have:
- Access to water and stay hydrated;
- Adequate rest time and take regular breaks; and
- Access to the shade whenever possible.
- Employers also can make sure that employees are properly acclimatized before engaging in strenuous activities.
States Considering Standards
On July 8, Oregon adopted a 180-day emergency rule protecting workers from indoor and outdoor heat. The requirements expand access to shade and cool water and include regular cool-down breaks, training, communication, emergency planning, and other measures. It also uses a tiered system with requirements starting up once the heat index is at 80 degrees and increasing when the heat index reaches 90. This temporary standard likely will be the basis of a permanent one to be adopted in the fall.
Virginia is drafting a standard with an intent to “reduce/eliminate employee injuries, illnesses, and fatalities due to exposure to excessive heat at indoor and outdoor places of work.”
General Duty Clause
Historically, OSHA has protected workers against extreme heat by using the General Duty Clause, a “catch-all” provision in the Occupational Safety and Health Act that requires employers to provide employment and places of employment that are free of recognized hazards, which, in the past, has included heat exposure. OSHA noted that in a 2019 case, A.H. Sturgill Roofing Co. v. Secretary of Labor, the Occupational Safety and Health Review Commission (OSHRC) set a high bar for use of the General Duty Clause in cases involving heat exposure and other potentially dangerous environmental conditions. In 2020, an OSHRC judge followed Sturgill and overturned five heat hazard citations against the U.S. Postal Service, holding that OSHA could not rely on a National Weather Service guide to determine heat severity.
OSHA Recommendations
Currently, OSHA recommends that employers set thermostats between 68 degrees and 78 degrees Fahrenheit. OSHA also provides guidance on “Working In Outdoor and Indoor Heat Environments,” and it suggests that employers:
- Provide workers with water and rest.
- Allow new or returning workers to gradually increase workloads and take more frequent breaks as they acclimatize or build a tolerance for working in the heat.
- Plan for emergencies and train workers on prevention.
- Monitor workers for signs of illness.
Author: By Courtney M. Malveaux
You might also like
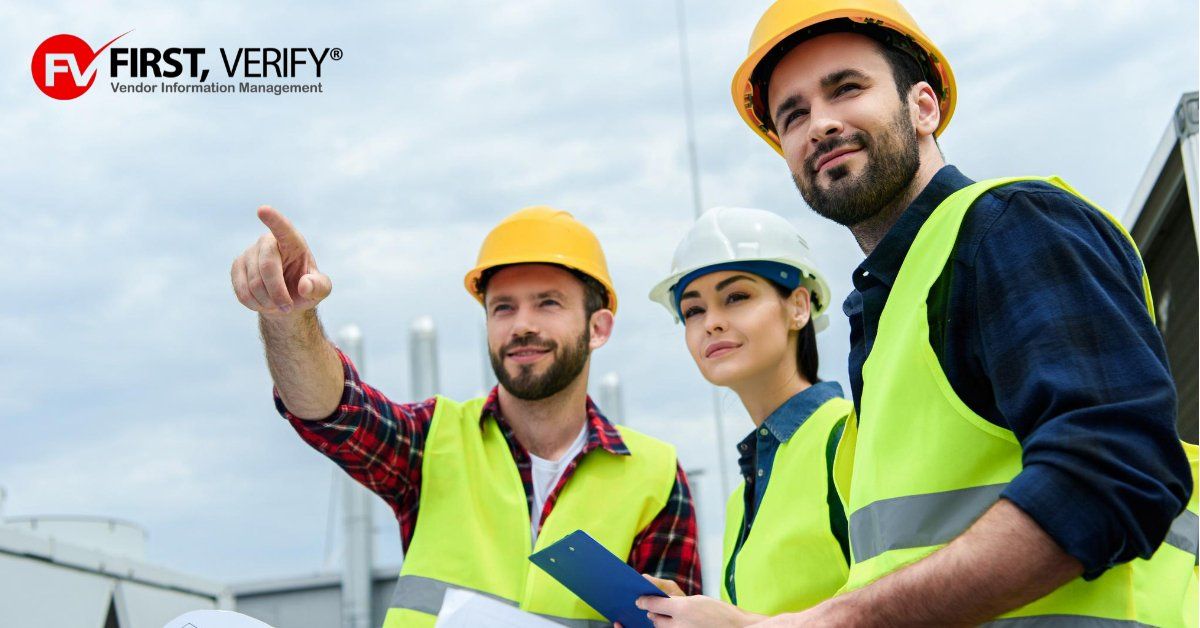