The Case for Prequalifying Contractors and Suppliers
Prequalification is most commonly used for contractors, but there is an increasing demand to prequalify supply vendors as well. This article will focus primarily on the need to prequalify contractors.
Accidents happen every day and current statistics say that human error is the cause of over 85% of those accidents. For ever 300 near-miss incidents, there are an average of 29 minor injuries and one serious injury or fatality.
Many companies have implemented a strong internal safety program and some have even created a culture of safety. Their losses are lower than the average stated above which, of course, brings the averages down — a good thing.
The problem comes with the introduction of outside contractors. Since they are not part of your organization, the question becomes what additional risk, if any, do they introduce into your company’s work environment?
- Smart risk and safety managers should be wondering about the consequences of:
- Signficiant damage to the facility
- Serious injuries, or worse, fatalities
- The contractor at fault having no insurance coverage
- Having to pay the price personally (loss of job or reputation)
- Companies that aren’t prequalifying their contractors generally fall into one of two camps. The first group feels that safety is the responsibility of the contractor. This is most often the case when new construction is taking place. That approach doesn’t meet OSHA requirements.
One company we are aware of delegated all the responsibility for safety on the construction site to their general contractor. Unfortunately, there was a fatality and, when OSHA investigated, they fined not only the general contractor but also the owners who had hired him. They stated that is was the company’s project on company property and, as such, the company had a duty to ensure that everyone on the project followed proper safety protocols.
The second group feels that they “know” their contractors because they have worked with them before and there is no need to look any further. One ethanol producer we know felt the same way. Unfortunately, a contractor who worked for them sent a new employee to their facility with no safety training. He fell through a grate onto the conveyer that led to the hammer mill. Fortunately for him, he was overweight and got jammed in the system. During the rescue, the ethanol company’s employees pulled on both his arms, dislocating both shoulders and doing permanent damage. As the ambulance drove away, they called the contractor to suggest he get in touch with his insurance agent. That was when they discovered he had let his insurance lapse. As you might guess, the employee’s attorney sued everyone and it took three and a half years in court to resolve the case. The ethanol company’s insurance covered all but their deductible. However, the lost time, damage to their reputation, and increased insurance costs were significant.
Losses caused by outside contractors or suppliers are bound to happen. The real question is how can you minimize the impact to your organization?
Companies often set up standards that any contractor who is going to work at their facilities must meet. Those standards almost always include a given level of insurance coverage and some documentation of safety programs, policies and, most importantly, safety history. The problem is that the task of gathering that information is often disseminated among different departments and even different facilities. To compound the problem, the various tasks are typically a part-time job function of the individuals charged with gathering the information. Unfortunately, this is where the process breaks down. As a part-time task, gathering the appropriate information receives all the efficiency and accuracy of a part-time effort. Even worse, if the tasks are distributed among various departments and facilities, the usual result is disconnected siols of data with no central location for people to access the needed information.
The common belief is that the system is in place and that any contractor performing work has been vetted and meets all the standards. The reality is usually quite different. Audits of these systems typically find that a large percentage (sometimes as high as 70%) are out of compliance with one or more of the standards. Frequently, critical documents like certificates of insurance have expired or the minimum coverage and required endorsements aren’t in place.
If you want an internal system, it should be housed in one location and have a minimum of two employees trained to gather, update, and determine a status for each contractor. Ideally, the system will be online and available to employees when they need it.
Using a third-party company to prequalify contractors can solve many of the challenges associated with an internal system. Some examples are:
- All contractors are vetted to the same standards
- Automated notifications and changes of status based upon expiration dates
- Electronic notifications sent to critical parties
- All the data is in an online, easy-to-access database that is accessible whenever the information is needed
- Your staff can focus on their core functions, making them more productive
- There is no duplication of effort
- The contractor has a single point of contact
- Phone and online support for both the client and the contractor
- System provides search capabilities, like who is prequalified and does the desired type of work
- Reporting capabilities are built in
- Often other services like background checks, score-carding, and online training are offered
- Online management and access of critical documents like:
- Certificates of Insurance
- NCCI letters
- OSHA 300 logs
- General Conditions Agreements
- Other critical documents
- The cost is borne by the contractors and suppliers
- Live customer support for both the client and the contractor
A third-party solution is often preferable sinc eprequalifying is typically not a core competency of most companies. Employees usually want relief from the nightmare of trying to obtain, update, and review all the information required.
Ready to simplify your safety program? Contact us today to learn more about smarter contractor/supplier management and how to close risk management gaps.
You might also like
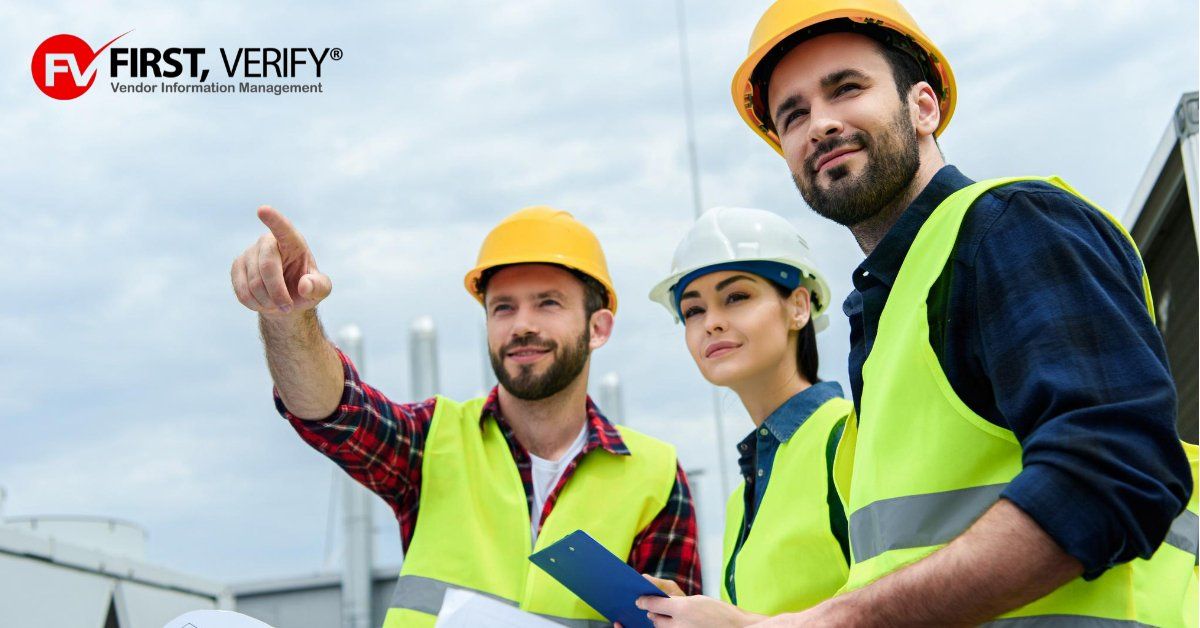