Expert tips
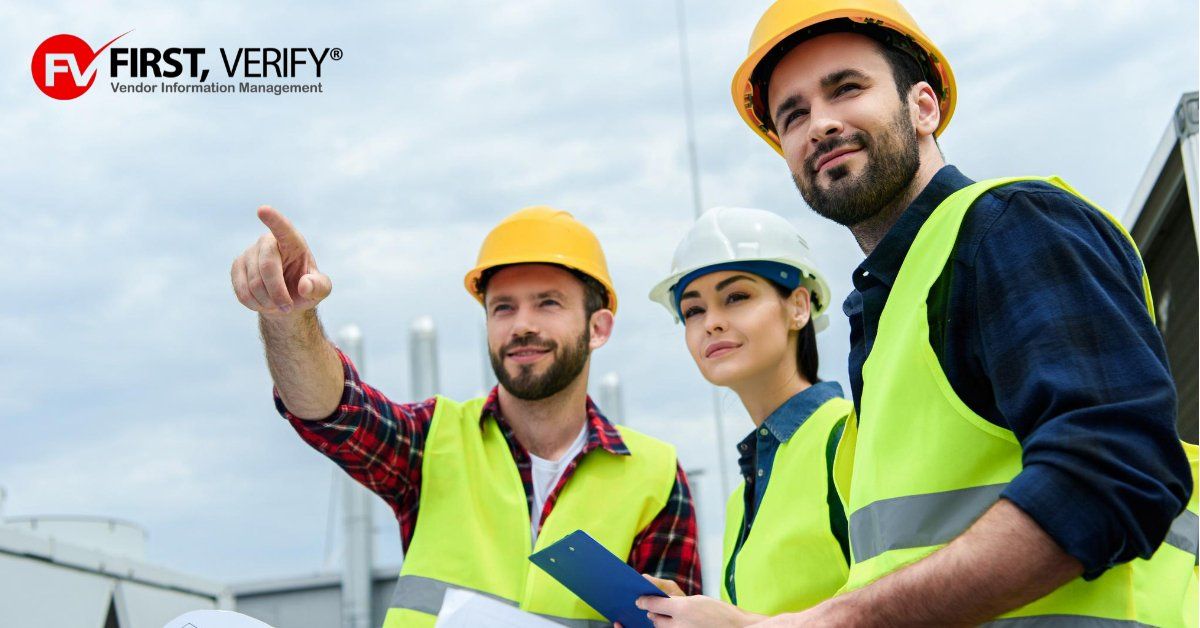
When a subcontractor is having trouble completing its subcontract work, it is not uncommon for a contractor to assert itself more directly into the completion process to help expedite the work. What’s the harm you might ask? A recent Loudoun County, Virginia case answered that question: It could lead to tortious interference with contract and conspiracy claims by the subcontractor. That case was Evans Construction Services (the subcontractor) versus Ox Builders (the contractor), and it also included a claim by the subcontractor against the contractor’s site superintendent, Lawler, as a co-defendant in the case individually. Evans alleged that Ox and Lawler tortuously interfered with Evan’s subcontracts by dealing directly with the subcontractors and directing the subcontractors’ work, cutting Evans out of the picture. Evans sought to recover its lost profits. Ox and Lawler argued against liability because Evans’ claims sought redress outside of Evans’ subcontracts with Ox and because Evans had no contract with Lawler at all, moving to dismiss Evans’ lawsuit as a matter of law. The court denied that motion, holding that the facts as pled by Evans were legally sufficient if ultimately proven by Evans, to support a claim for breach of legal duties separate from duties arising contractually only; and specifically for wrongful interference with Evans’ subcontracts and Evans’ related conspiracy claim against the defendants. Although the court acknowledged that Evans’ claims were interrelated with the Ox – Evans subcontracts underlying the parties’ relationship, those common facts could support both contractual and non-contractual breach claims in certain circumstances. The court further determined that such circumstances, if ultimately proven, included Evans’ claims that Ox and Lawler violated their independent common law duties to not interfere with Evans’ lower tier subcontracts and not conspire together to injure Evans in its business. The court, therefore, allowed Evans’ claims to proceed to trial on their merits. The defendants apparently did not argue to dismiss the conspiracy claim on the basis Lawler, as an employee of Ox, could not conspire with Ox, his employer (referred to as the intercorporate immunity doctrine), or at least that defense was not discussed in the court’s decision. But, regardless, this decision reflects the necessity for caution “going around” subcontractors when subcontract disputes arise. Author: Neil S.Lowenstein
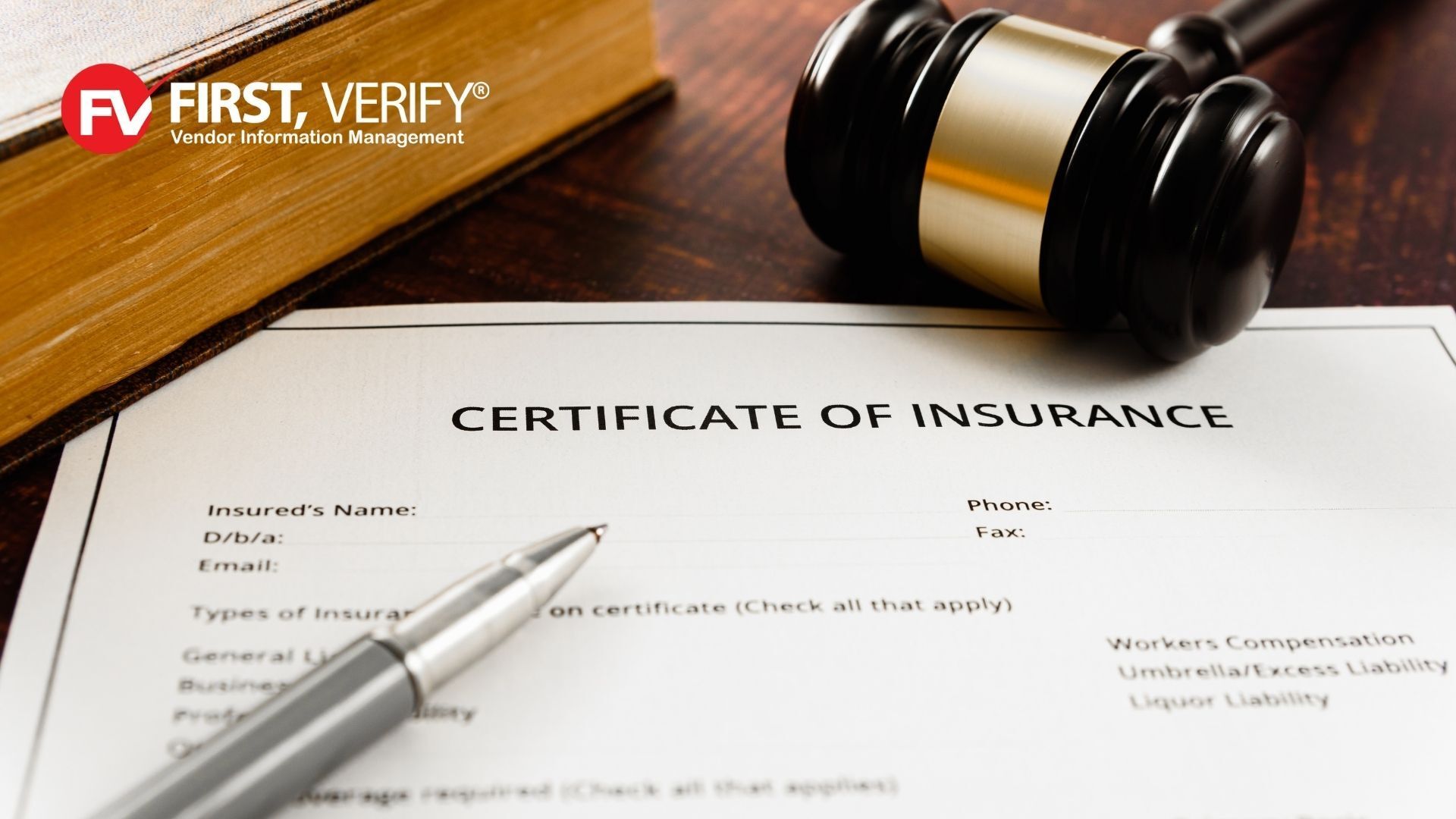
Collecting and making sure that Certificates of Insurance (COIs) are accurate and up-to-date is an enormous task, especially when you do not have tools to streamline this process. On top of this, checking to make sure you are not receiving fake insurance certificates is difficult. Here are a few best practices to follow when checking the authenticity of a COI. 1. Look for “Acord 25” The most common insurance certificate used by trustworthy insurance agencies is Acord 25. A real Acord form will have the Acord logo in the upper right-hand corner and the text “Acord 25” in the bottom left-hand corner. If the words “Acord 25” cannot be found in these places on the form, that is a red flag that this is not a legitimate insurance certificate. 2. Look for Consistent Handwriting & Font Looking at the expiration dates on insurance certificates you receive is a good place to check for fraud. If the dates are not in the center of the box or if they are in a different font than the policy number, there is a good chance the COI is a fake. Keep a lookout for anything handwritten or in a font that does not match the rest of your form. This is a good indicator of a fake insurance certificate. 3. Call the Insurance Company & Make Sure They are Legitimate If you have a bad feeling about a COI, you receive, call the insurance company that issued it. If the company does not answer or if the agent you get in contact with does not want to talk to you or seems hesitant, this is a red flag. If you do not recognize the insurance company listed in the upper right of the certificate, call your insurance agent to make sure they are a legitimate company. AMBest.com is also a good place to check the status of an insurance company. Use their “ratings and analysis” section to look up the insurance company in question and see if they are legitimate. 4. Understand the Layout The layout of COIs is complex, and somebody creating a fake likely will not know how to fill out the form. Look for these sections in Acord 25 forms: General liability Worker’s compensation Automobile liability These are common types of coverage you can expect to see on most forms. If you see coverage like Cyber Liability, make sure this coverage is part of the insurance policy. If there is coverage listed in the COI that you cannot find in the insurance policy, the COI is probably a fake. It is also important to look out for things like zeroes, N/A, or None listed when there is coverage not included in the policy that is present on the COI. On an actual proof of insurance certificate, these boxes will be left blank to state the limit. 5. Make Sure the Insured Box is Filled Out Correctly The name in the insured box on an insurance certificate should be the name of the business, not a person’s name. The business address should also be in the box. It is important to check this section when looking for a fake COI because if an inexperienced person filled out the form, they will probably put their name in this section. Another important reason to check this box is to make sure coverage is afforded in the case of a real insurance certificate. If the name in the box is not correct, coverage may not apply when a claim is made. 6. Look for the Right Contact Information The contact information on an insurance certificate should be the information of the insurance agent or broker who issued the form. If this information is instead for the person who is covered by the certificate, they probably filled out the form on their own. The signature at the bottom of the certificate should also match the name in the contact information box. Lastly, the email domain in the contact information should match the name of the Producer of the certificate, that is the name of the insurance company. If any of this information seems off, do a quick search online to make sure the person who created the COI works for the Producer or call them to confirm. If you are unsure of how to identify a fake COI and keep track of your contractor’s insurance policies, check out FIRST , VERIFY’s COI Management web application . Find out how we can help you reduce the risk associated with fake policies and increase compliance at all times.
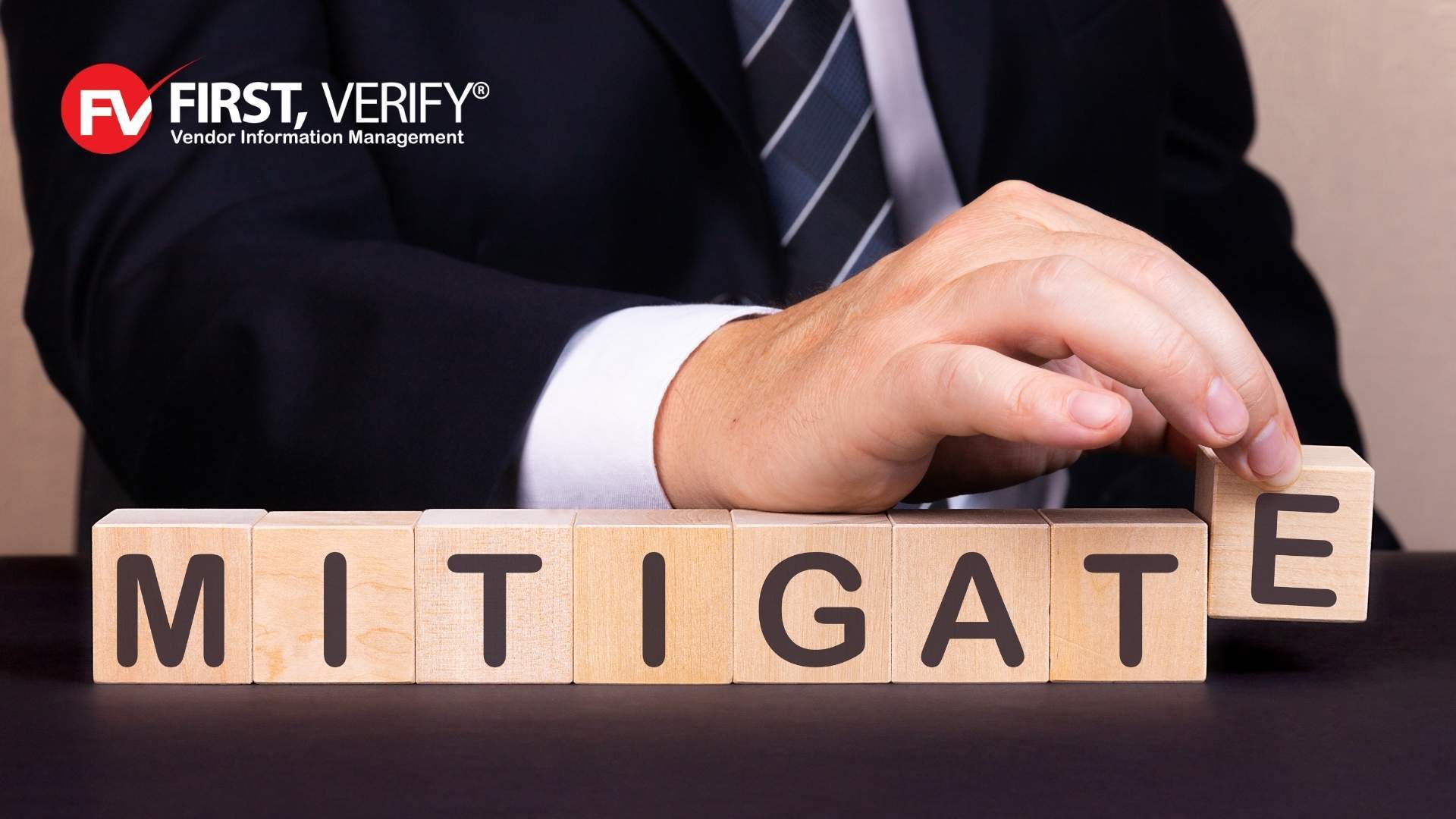
Every entrepreneur and business leader are looking to grab any technology-driven advantage they can as they adapt to new ways of working, managing employees, and serving customers. At the same time, they are trying to manage risk — and the same digital initiatives that create new opportunities can also lead to risks such as security breaches, regulatory compliance failures, and other setbacks. The result is an ongoing conflict between the need to innovate and the need to mitigate risk. Mitigating risks is one of the most important jobs that management has to deal with on daily basis. With efficient and smart use of the technology of today, the everyday risks of the business can be greatly reduced. Here are a few ways that technology can help mitigate risks: Security: Security is an extremely important aspect of a business this is because almost all businesses have sensitive information and failure to keep them secure could result in disastrous events if the wrong people get their hands on it. Losing a file from the cabinet, or a floppy disc, or even a stolen laptop containing crucial information can make the owners go berserk. But now, thanks to technology, it is ensured that only relevant and right people can access the information they need. Now there are unique passwords and codes to keep sensitive information safe. Even facial recognition can prevent the theft of data leading to operational risks. Technology has made it tough for wrongdoers to indulge in malicious behavior. The fear of being tracked and getting caught is pervading. Access: Access is another facet that is often misused and is easily hacked. Some people need to have instant access to important information so that crucial decisions can be made right away. These decisions affect the well-being of the company. This access needs to be limited to certain members of the management team only as they are responsible for carrying out the smooth operations of the business. Numerous software and cloud-based technology allow the management to access real-time information right away from anywhere. The technology ensures that all the information is monitored tightly. Profit Loss: Generating sales and making profits is the main goal of a business that holds the entire process together. With the usage of robust technology systems, the areas of concern can be properly focused on. Using the right technological solutions in office management software as well as other activities allows businesses to know where the resources and finance are being utilized and a proper picture of profit and loss can be attained. Irregularities in record-keeping indicate fraudulent activities by vendors, employees, or both. Efficient Use of Time: Time is an important element in every walk of life. And when important business decisions have to be made, time becomes paramount. That's why a business demands that all of the employees use their time productively for organizational growth. A profitable business asks its employees to direct their talents and energies into tasks that bring something to the business. The right kind of technological solution will act as a watchdog to monitor transparency within the business operations, process streamlining, and efficient use of employee energy. Expense Management: Businesses have to follow a budget closely so to maximize their profits. They cannot be callous about cost and follow the saying- 'a penny saved, is a penny earned'. When there is no communication between departments or lack of proper filing, paperwork, or recordkeeping mistakes can occur resulting in false numbers; with the help of technology like using an asset management system, the process goes out without a hitch giving clarity on how much expenses are occurring and where. All organizations face uncertainty. The effect this uncertainty has on an organization's objectives is referred to as "risk." The challenge for management is to determine how much uncertainty or risk to accept and how to manage it to an acceptable level. Technology has been a blessing for all. It monitors, reviews, guards any loss of data, unnecessary expenses, false information, and a myriad of other aspects. Technology not only finds the culprits in case of wrongdoing harming a business, but it also allows any issues to be identified early and address them immediately. FIRST, VERIFY is a one stop solution for companies across industries to mitigate risk be helping develop and execute a strong risk mitigation strategy and a robust technological solution. Read more about our risk mitigation services here .
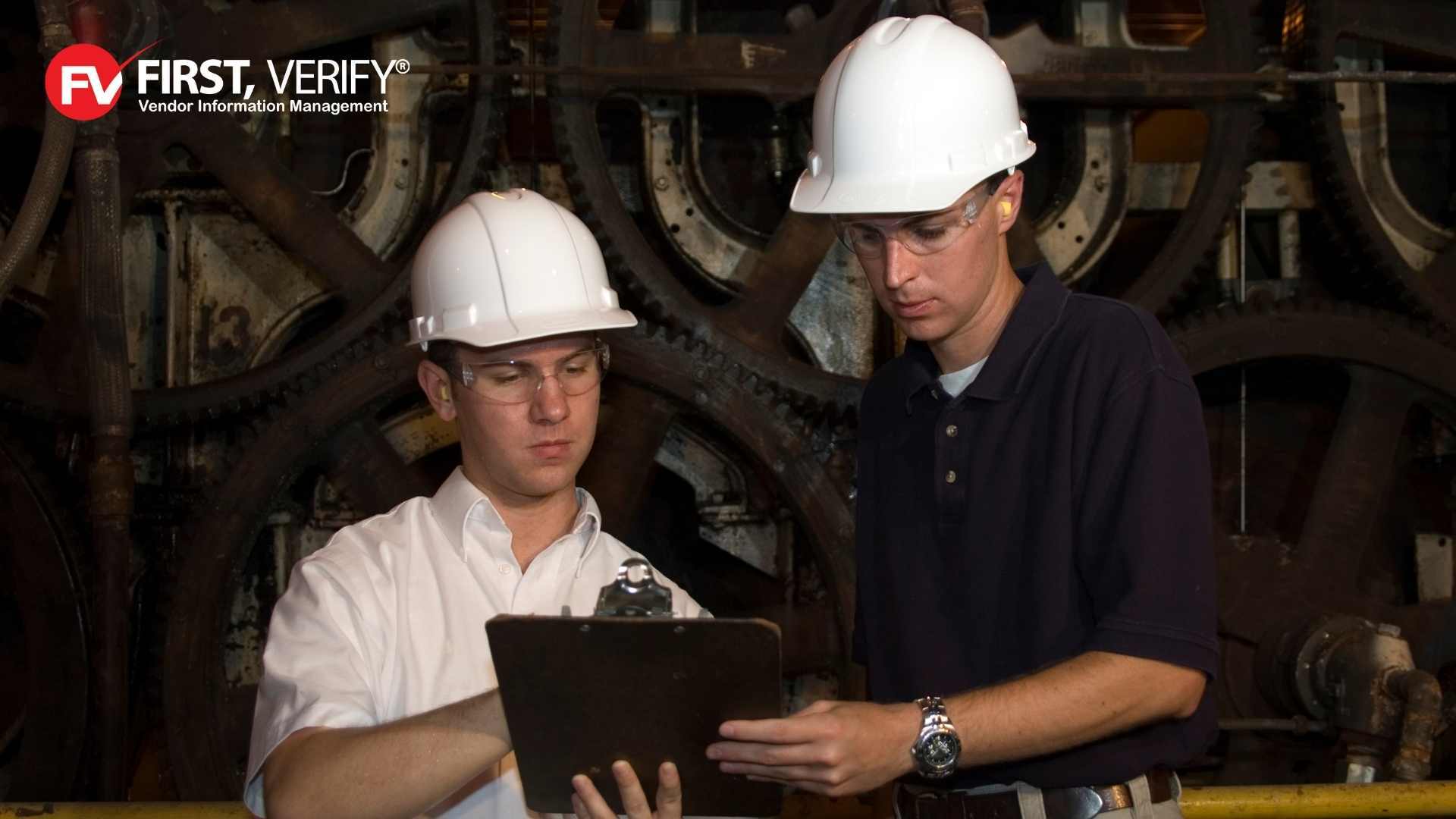
This past spring, the Occupational Safety and Health Administration (OSHA) announced its intention to implement a new heat illness standard that will apply to indoor environments. The agency said it has manufacturing facilities in mind, as the rule targets “indoor workers without climate-controlled environments.”